RARE EARTH PROCESSING FACILITY RADIOLOGICAL DECOMMISSIONING
Industry: Manufacturing
Location: Gulf Coast
Innovative Remediation Strategies Achieves Client’s Goals and Cost Savings
ENTACT decommissioned, decontaminated, and demolished a former rare earth minerals processing plant within a larger chemical manufacturing complex. The site received USEPA closure approval in 2015. Through modeling, remediation goals were established for allowable soil concentrations, achieving regulatory compliance with limits of 3 pCi/g for thorium-232 and 9 pCi/g for uranium-238. 100,000 tons of radiologically impacted soil, sediment, and construction debris and 230,000 gallons of impacted water were removed from the facility using rail, truck, and tanker transport. Waste was disposed of at four different facilities nationwide, depending on contamination levels. ENTACT performed the following work:
- Conducted a 1,500-sample characterization plan pre-excavation across the 13-acre site
- Surveyed, demolished, and sorted impacted structures, roadways, and paved surfaces for disposal based on radiological activity, recycling materials when possible
- Constructed a one-acre, five-million-gallon temporary fire water pond lined with HDPE for fire protection; remediated the two-acre fire water pond
- Dewatered, characterized, and transported sediments from four wastewater processing ponds containing NORM-impacted materials, while keeping ponds in service; reconstructed ponds with new clay and synthetic liners to optimize water management
- Hydro-blasted 3,500 linear feet of storm sewer with combination air-movers
- Conducted radiological gamma surveys in-situ upon completion
- Demolished a 5,000-square-foot laboratory, recycling multiple chemicals and lab equipment or transporting them for disposal
- Conducted area-wide sampling after excavation using GPS gamma surveys for MARSSIM closure and final status reporting
- Produced sample logs and zone heat maps for regulatory compliance
- Sampled pond sediment in-situ for disposal profiling; solidified onsite and loaded directly into 20-yard tractor-trailer dump trucks
- Re-evaluated large excavation methods into small grids with limited open durations, using tarps to control rainwater contamination
- Achieved a project variance through detailed site characterization and negotiations with state regulators, allowing a gradient scale for final material retention on site
Sustainable Remediation Practices
- Reduced transportation costs contributed to decreased carbon emissions
- Recycled lab chemicals and equipment to lower disposal costs
Let’s work together
We want to hear about your project. Learn how we
deliver results with innovation.
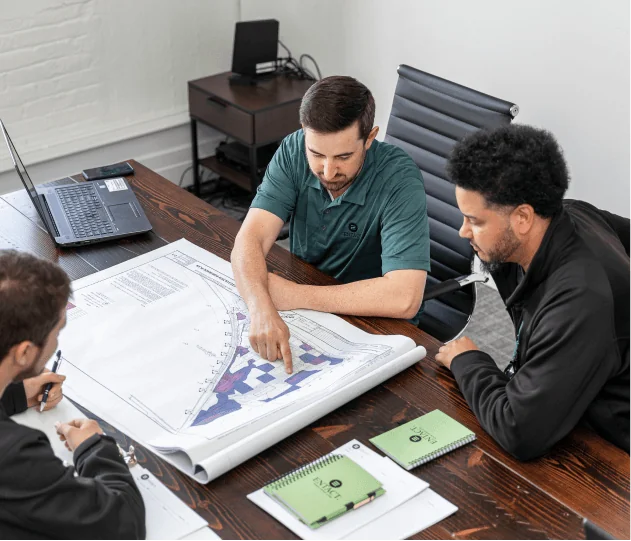